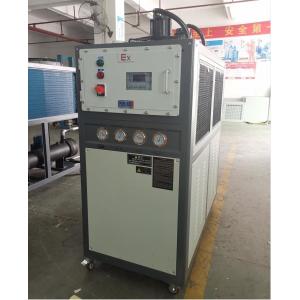
Add to Cart
JLSF-10AD Explosion-Proof Water Chiller Oil And Gas Processing, Equipment Cooling, Tunnel Ventilation Systems
Product Description:
Explosion-proof chiller is a cooling equipment specially designed for flammable and explosive places. Its main components include compressors, motors, condensers, evaporators, etc. Explosion-proof chillers adopt explosion-proof design components mainly include the following aspects:
1. Explosion-proof motor: The motor of the explosion-proof chiller adopts an explosion-proof motor, and its shell and wiring are made of explosion-proof materials to prevent the spark of the motor from causing an explosion.
2. Explosion-proof compressor: The compressor of the explosion-proof chiller adopts an explosion-proof compressor, and its internal mechanical and electrical components adopt explosion-proof design to ensure its safe operation in an inflammable and explosive environment.
3. Explosion-proof condenser: The condenser of the explosion-proof chiller adopts an explosion-proof condenser, and its material and structure are specially designed for flammable and explosive environments to prevent it from causing an explosion.
4. Explosion-proof evaporator: The evaporator of the explosion-proof chiller also uses an explosion-proof evaporator, and its special material and structure can operate safely in a flammable and explosive environment.
It should be noted that the explosion-proof design of the explosion-proof chiller needs to be selected and designed according to the specific use occasions and needs to ensure that the equipment can achieve the best explosion-proof effect. At the same time, when using an explosion-proof chiller, it is also necessary to operate in accordance with relevant safety regulations and operating requirements to ensure the safety of the equipment.
Production Features:
Explosion-proof chiller is a kind of cooling equipment specially designed for flammable and explosive places. Its main features include the following aspects:
1. Explosion-proof design: The explosion-proof chiller adopts an explosion-proof design. Its main components, such as motors, compressors, and condensers, are designed with explosion-proof materials and structures, and can operate safely in flammable and explosive environments.
2. High efficiency and energy saving: Explosion-proof chillers use high-efficiency compressors and condensers, which have high cooling efficiency and can save energy.
3. Flexible installation: The explosion-proof chiller can be installed indoors or outdoors, and the type selection and installation can be carried out according to specific needs.
4. Simple maintenance: Explosion-proof chillers are relatively simple to maintain, and only need regular cleaning and maintenance, which is relatively easy to maintain.
5. High temperature control accuracy: The explosion-proof chiller is equipped with a precise temperature control system, which can achieve precise temperature control.
6. Wide range of applications: Explosion-proof chillers are suitable for flammable and explosive places such as petrochemical industry, coal mine, pharmaceutical manufacturing, and painting.
It should be noted that the selection and installation of explosion-proof chillers need to be selected and designed according to specific usage occasions and needs to ensure that the equipment can achieve the best explosion-proof effect. At the same time, when using an explosion-proof chiller, it is also necessary to operate in accordance with relevant safety regulations and operating requirements to ensure the safety of the equipment.
Working Principle:
The working principle of the explosion-proof chiller is basically the same as that of the ordinary chiller, but a series of explosion-proof measures have been taken in the design and construction to ensure safe operation in hazardous environments. The following is the general working principle of explosion-proof chillers:
1. Cooling cycle: The explosion-proof chiller absorbs the heat generated in the equipment or process through the circulating medium (usually water or other cooling liquid), and takes it to the cooler for heat dissipation, and then the cooling medium circulates back to the equipment for cooling .
2. Compressor: The chiller contains a compressor inside, which compresses the refrigerant so that it becomes a high-temperature and high-pressure gas under high pressure.
3. Condenser: The high-temperature and high-pressure gas passes through the condenser, contacts with the cooling medium and releases heat, cooling the refrigerant and turning it into a liquid state.
4. Expansion valve: The liquid refrigerant enters the evaporator through the expansion valve. The function of the expansion valve is to reduce the pressure and temperature of the refrigerant so that it becomes a low-temperature and low-pressure evaporated gas.
5. Evaporator: The low-temperature and low-pressure evaporated gas passes through the evaporator, contacts the equipment or process to be cooled, absorbs heat and cools it down.
In the explosion-proof chiller, the key to the working principle is the explosion-proof design and construction. The following are
some common explosion protection measures:
- Explosion-proof electrical components: Use explosion-proof motors, switches, sensors, etc. to prevent explosions caused by electric sparks.
- Explosion-proof shell: The shell of the chiller adopts an explosion-proof design, which can withstand internal pressure and temperature, and prevent external flammable gases from entering the interior.
- Explosive gas discharge: The discharge of explosive gas is considered in the design of the chiller to release the explosion pressure beyond the safe range.
- Material selection: Use high temperature resistant, anti-corrosion and explosion-proof materials to ensure that the chiller can withstand and prevent explosion risks in hazardous environments.
The above is the general working principle and common explosion-proof measures of explosion-proof chillers. The specific working principle and design details may vary due to different explosion-proof standards and application requirements.
① Compressor | ⑤ Evaporator | ⑨ Temperature sensor | ⑬ Bypass valve |
② Condenser | ⑥ Ball valve | ⑩ Water tank | ⑭ Low voltage controller |
③ Filter drier | ⑦ Antifreeze switch | ⑪ Water pump pressure gauge | ⑮ High voltage controller |
④ Expansion valve | ⑧ Float switch | ⑫ Water pump | ⑯ Fan |
Techinical Parameters:
Model | JLSF-5HP | JLSF-10HP | JLSF-15HP | JLSF-20HP | JLSF-25HP | JLSF-30HP | JLSF-40HP | JLSF-50HP | JLSF-60HP | ||
Cooling capacity | KW/h | 15.5 | 31 | 46.5 | 65 | 77.5 | 93 | 124 | 155 | 186 | |
Kcal/h | 13,750 | 27,500 | 41,250 | 55,000 | 68,750 | 82,500 | 110,000 | 137,500 | 165,000 | ||
Temperature range | 5℃-35℃(Below 0℃ can be customized) | ||||||||||
Power supply | 1N-220V 50HZ/60HZ 3N-380V/415V 50HZ/60HZ | ||||||||||
Total power | KW | 4.5 | 8.83 | 13.62 | 19.8 | 22.75 | 28.3 | 39.2 | 46.75 | 56.1 | |
Compressor | Type | Hermetic scroll type or piston | |||||||||
Power | KW | 3.75 | 7.5 | 11.25 | 15 | 18.75 | 22.5 | 30 | 37.5 | 45 | |
Circulating pump | Power | KW | 0.75 | 1.5 | 1.5 | 2.2 | 2.2 | 4 | 4 | 4 | 5.5 |
Head | m | 22 | 21.5 | 21.5 | 22 | 22 | 25 | 25 | 25 | 26 | |
Refrigerant | Type | R22/R407c/R134a/R410a | |||||||||
Control method | Temperature Sensing External Pressure Equalizing Expansion Valve | ||||||||||
filling volume | Kg | 3.2 | 6.4 | 9.1 | 12.2 | 15.3 | 18.6 | 24.5 | 30.6 | 36.8 | |
Evaporator | Flow | m³/h | 2.42 | 4.85 | 7.6 | 10.16 | 12.34 | 15.2 | 19.53 | 23.3 | 30.52 |
water capacity | m³/h | 0.65 | 0.18 | 0.21 | 0.28 | 0.32 | 0.32 | 0.61 | 0.66 | 0.72 | |
Diameter | inch | 1" | 1.5" | 2" | 2.5" | 3" | |||||
Condensator | Type | Efficient brass sets corrugated aluminum fin | |||||||||
Fan | Type | Axial flow | |||||||||
air volume | m³/h | 5000 | 10000 | 15000 | 20000 | 25000 | 30000 | 40000 | 50000 | 60000 | |
Protective device | High and low pressure switch, antifreeze protection, fusible plug/safety valve, overload protection device, coil overheat protector, automatic temperature protection switch, etc. | ||||||||||
Machine size | L | mm | 1140 | 1400 | 1750 | 2000 | 2000 | 2200 | 2000 | 2000 | 2400 |
W | mm | 620 | 725 | 750 | 900 | 900 | 900 | 1800 | 1800 | 1800 | |
H | mm | 1200 | 1450 | 1500 | 1770 | 1770 | 1770 | 2200 | 2300 | 2300 | |
Unit weight | Kg | 230 | 410 | 540 | 660 | 720 | 910 | 1120 | 1400 | 1560 |
Application Industry:
Explosion-proof chillers are mainly used in the following industries, which have high requirements for equipment safety and explosion-proof capabilities:
1. Chemical industry: The chemical industry involves many flammable and explosive substances, such as chemical production, petroleum refining, paint manufacturing, etc. Explosion-proof chillers can be used to provide safe cooling and temperature control for chemical equipment and processes.
2. Oil and gas industry: During oil and gas extraction, storage, transportation and processing, there are risks of explosion and fire. Explosion-proof chillers can be used to provide cooling and temperature control to ensure safe operation of equipment in hazardous environments.
3. Pharmaceutical Industry: Certain chemicals used in pharmaceutical processes can be explosive or flammable. Explosion-proof chillers can be used to provide safe cooling and temperature control for pharmaceutical equipment, ensuring pharmaceutical process safety and product quality.
4. Electronics and semiconductor industry: Chemical substances and equipment used in the electronics and semiconductor manufacturing process may present risks of explosion and fire. Explosion-proof chillers can be used to provide cooling and temperature control for electronic equipment and semiconductor manufacturing equipment, ensuring the safety of the production environment.
5. Automobile manufacturing industry: Automobile manufacturing involves various painting, spraying and drying processes, and the spray paints and solvents are flammable. Explosion proof chillers can be used to provide safe cooling and temperature control for painting and drying equipment.
6. Coal mines and mining industry: There is a risk of accumulation and explosion of combustible gases in coal mines and mines. Explosion-proof chillers can be used to provide safe cooling and temperature control to ensure the safe operation of mining equipment and processes.
Explosion-proof chillers have special safety design and explosion-proof measures, such as the use of explosion-proof electrical components, high-temperature-resistant materials, explosion-proof enclosures, etc., to reduce the risk of explosion or fire caused by equipment in hazardous environments. In these industries, explosion-proof chillers are important equipment to ensure process safety and protect personnel's lives and property.
Automotive Manufacturing Chemical Engineering Electronics Industry Electroplating Industry
Injection Molding Industry Pharmaceutical Industry Plastic Packaging Industry Printing Industry
Upport and Services:
Chiller technical support and service includes:
1. 24/7 customer support
2. Remote guidance installation and maintenance
3. Remote Diagnostics and Troubleshooting
4. Phone/Email Advice and Guidance
5. User friendly documentation and manuals
6. Software Updates and Upgrades
7. Cost price of spare parts and consumables
Packing and Shipping:
Chillers are packaged and shipped in standard plywood wooden boxes. All components are secured and protected with a film, and the unit is then placed on a pallet for easy transport. And affix the shipping mark information label on the wooden box to ensure correct delivery.
How safe is the explosion-proof chiller?
The safety performance of explosion-proof chillers is through special design and construction to ensure safe operation in hazardous environments. The following are the safety performance considerations of explosion-proof chillers:
1. Explosion-proof design: Explosion-proof chillers adopt an explosion-proof design, including the use of explosion-proof housings, explosion-proof electrical components and explosion-proof materials. These design measures prevent sparks or other possible sources of explosion.
2. Compliance with explosion-proof standards: Explosion-proof chillers usually comply with specific explosion-proof standards and specifications, such as the explosion-proof standards of the International Electrotechnical Commission (IEC), the European explosion-proof standards (ATEX), etc. They are rigorously tested and certified for safe performance in explosive atmospheres.
3. Explosion gas discharge: Explosion gas discharge is considered in the design of explosion-proof chillers, so as to release the explosion pressure beyond the safe range and reduce the harm to equipment and personnel.
4. Temperature and pressure monitoring: Explosion-proof chillers are usually equipped with temperature and pressure monitoring devices, which can monitor the working status of the equipment in real time. Once the temperature or pressure exceeds the safe range, it will trigger an alarm or automatically stop to avoid potential danger.
5. High-temperature-resistant materials: Explosion-proof chillers use high-temperature-resistant materials, which can maintain structural stability and integrity in high-temperature environments and reduce safety hazards caused by high temperatures.
6. Overload protection: Explosion-proof chillers usually have an overload protection function. When the equipment is overloaded or fails, it will automatically stop or take other safety measures to protect the safety of equipment and operators.
In general, explosion-proof chillers have been designed and constructed with special safety considerations to ensure their safe performance in hazardous environments. These safety performance measures are designed to reduce the risk of fire, explosion and other hazardous events and to protect the safety of equipment, workers and the environment.